QC Lab Study
Background
AVS Life Sciences delivers cutting-edge engineering, projectmanagement, automation, validation, and clinical solutions to clients in the pharmaceutical, biotech, medical device, and diagnostic industries. Our team goes beyond execution—we build lasting partnerships and ensure full traceability in every service we provide, from utilities support and preventive maintenance to installation and documentation.
We are proud of our 100% success rate across FDA, EMA, and PIC audits, a testament to our rigorous quality and compliance standards.
In this case study, we detail a complex, multi-year collaboration with a major pharmaceutical manufacturer to repurpose an underutilized room within an activeGMP facility—ultimately enabling a new continuous direct compression manufacturing process.
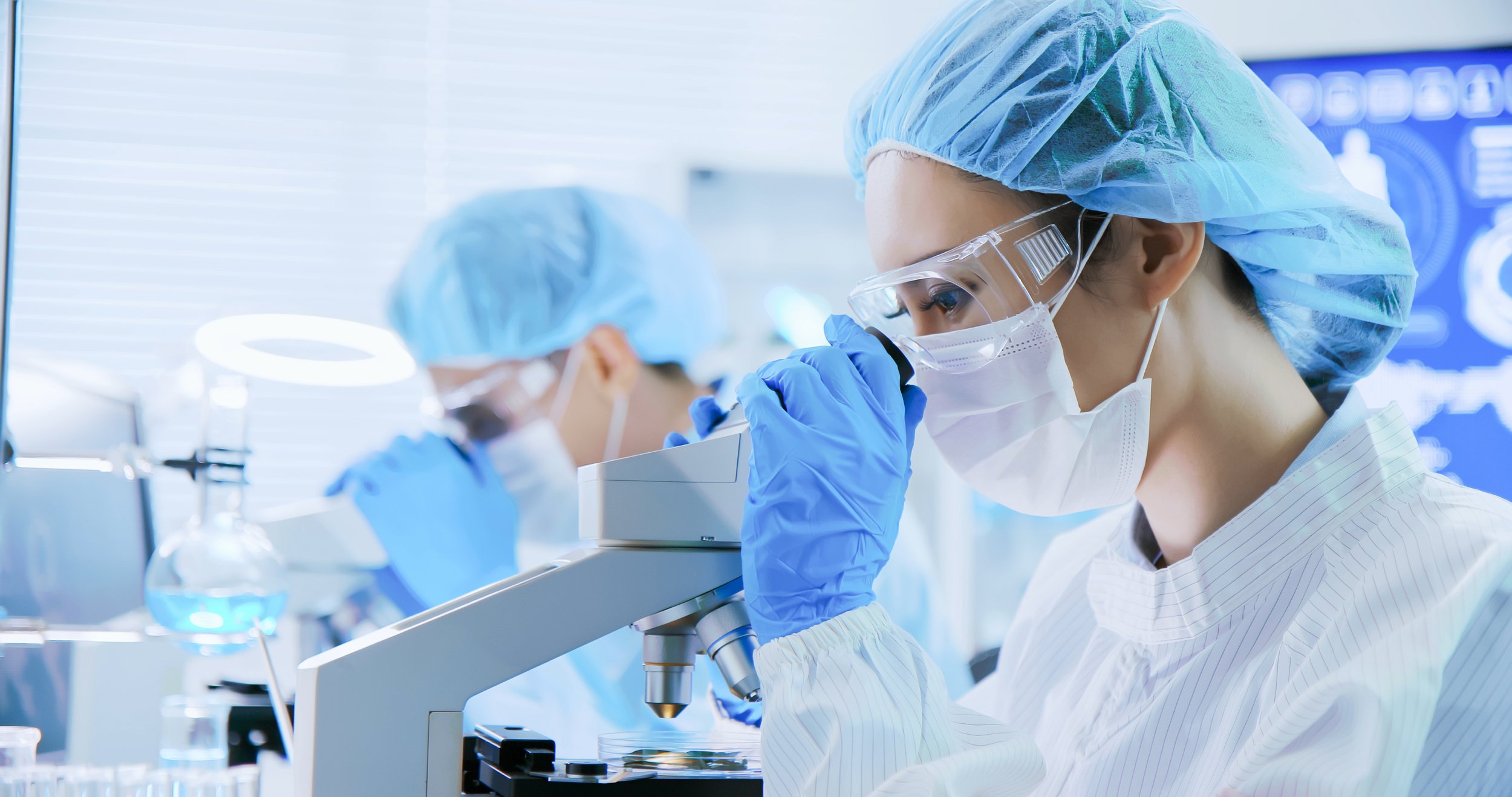
The client is a leading San Francisco based biotechnology company dedicated to pursuing groundbreaking science to discover and develop medicines for people with serious and life-threatening diseases such as targeted antibodies for cancer.
Laboratory process qualification and quality control (QC) and assurance are critical, particularly in highly regulated industries such as biotech. There are many definitions of quality, but in a laboratory setting, it generally refers to the accuracy and reliability of results. While inaccuracy is accepted to an extent, a strong quality management system will keep that level to a minimum.
Quality and compliance go hand in hand and can form the backbone of an organization's viability. Lack of QC and assessment can lead to dire consequences for organizations and their customers. Lab staff strive to meet quality and compliance standards to ensure outputs are reliable and conform to regulations.
AVS assisted our client in upgrading their manufacturing space from a Biosafety Level 1 GMP facility to a Level 2 GMP facility. We were able to complete the entire project on schedule and within budget. Moreover, our documentation efforts to demonstrate full traceability was deemed appropriate by our client’s quality assurance team.
We were able to support our client throughout this entire transition process, from gap analysis to final equipment installation. Because of our efforts, this pharmaceutical manufacturer was able to manufacture medication with the lentivirus vector material. This collaboration allowed our client to focus on what they do best – develop medicines to help improve their target patient’s quality of life.
While re-visiting some protocol tests initially tested by the technician, we observed some anomalies in test results that were shown as “Passed”. Upon further investigation it was found that the technician did not detect that some barcode scanner cameras were installed upside down.
This was overlooked because the barcode scanner returned sets of values of 0s and 1s that can sometimes give identical results depending on the barcode being scanned. This was also overlooked because there were not sufficient tests to challenge the system.
A positive outcome was that important lessons learned were captured for the client. This led the QC laboratory team and Quality team to evaluate their business process to identify the gaps that allowed for unreliable test results.
This experience also helped the team have open discussions regarding team workload, and responsibilities they have to each other, to the company and ultimately to the patients.