Understanding Current Good Manufacturing Practices in Pharma
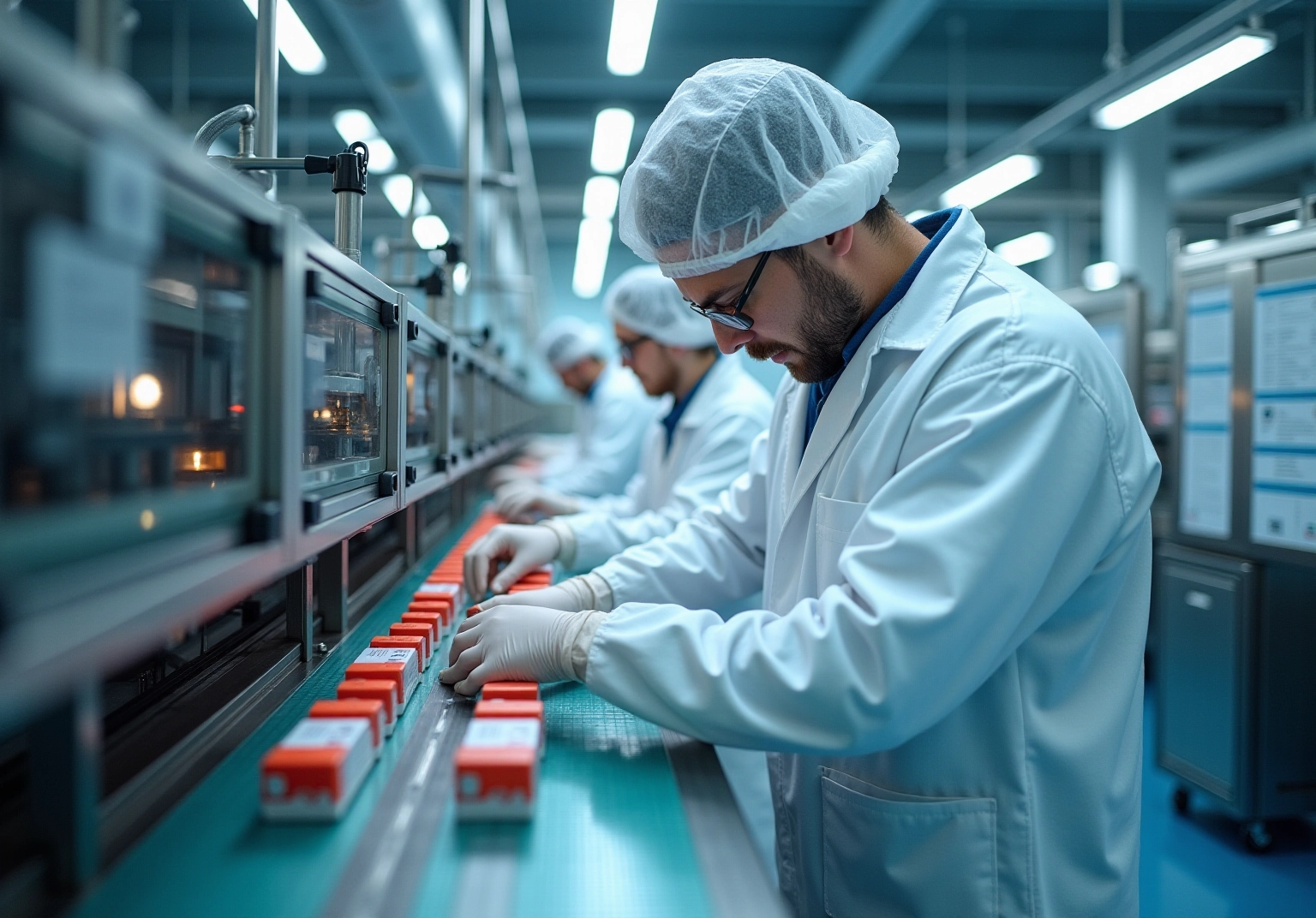
Overview
The article underscores the critical importance of Current Good Manufacturing Practices (cGMP) within the pharmaceutical industry. It emphasizes that adherence to cGMP is fundamental in ensuring product quality, safety, and compliance with regulatory standards. Notably, compliance with cGMP safeguards public health by preventing the distribution of contaminated or ineffective medications. Furthermore, it enhances operational efficiency and fosters consumer trust, as evidenced by various case studies and regulatory oversight data. This dual focus on quality and efficiency not only protects patients but also positions companies favorably in a competitive market, making cGMP adherence a vital consideration for industry stakeholders.
Introduction
Current good manufacturing practices (cGMP) are not merely regulatory requirements; they form the backbone of quality assurance within the pharmaceutical industry, guaranteeing that every medication produced adheres to the highest safety and efficacy standards.
As the biologics market expands, the complexities of complying with these regulations intensify, presenting both challenges and opportunities for pharmaceutical companies.
What are the ramifications when organizations fail to comply? The consequences can be severe, impacting not only public health but also the reputation and financial stability of the businesses involved.
Define Current Good Manufacturing Practices (cGMP)
Current good manufacturing practices are essential regulations established by the Food and Drug Administration to ensure the quality, safety, and efficacy of pharmaceutical products. These guidelines set the minimum standards for manufacturing processes, facilities, and controls involved in drug production. The term 'current' emphasizes the necessity of utilizing up-to-date technologies and methodologies to maintain compliance.
Regulations surrounding Good Manufacturing Practices encompass critical areas such as:
- Personnel qualifications
- Sanitation protocols
- Equipment maintenance
- Stringent quality control measures
These components are designed to prevent contamination and uphold product integrity, which is vital in an industry where the stakes are particularly high.
By 2025, the biologics market is projected to grow at a compound annual growth rate of 15%, which underscores the increasing complexity and the necessity for compliance with current good manufacturing practices. The FDA's unwavering commitment to enforcing these regulations is evident in the continuous updates and revisions to guidelines, ensuring that manufacturers are well-equipped to tackle evolving industry challenges.
The successful implementation of current good manufacturing practices is not just a regulatory obligation; it serves as a cornerstone of operational excellence in pharmaceutical production. Case studies illustrate that organizations that follow current good manufacturing practices not only enhance product standards but also achieve significant improvements in efficiency and compliance outcomes. For instance, a retrospective analysis of good manufacturing practices regulations over the past 30 years indicates that while larger companies have made notable advancements in statistical applications under these guidelines, there remains a critical need for uniform application across the industry.
The importance of cyclic guanosine monophosphate is further underscored by industry leaders advocating for a balanced approach to efficiency and quality enhancement. As Peter Drucker articulated, organizations must recognize that efficiency in tasks does not equate to their inherent value. This perspective is crucial as the medicinal landscape evolves, particularly with the advent of novel treatments such as monoclonal antibodies, which present unique challenges necessitating a robust quality management system.
In summary, GMP regulations extend beyond mere compliance; they are vital for ensuring that medical products are manufactured to the highest standards, safeguarding public health and maintaining trust in the industry. AVS Life Sciences, renowned for its commitment to excellence and an impressive 80% repeat business rate, exemplifies the effectiveness of adhering to these practices, positioning itself as a leading provider of management and regulatory compliance solutions in the life sciences sector.
Explain the Importance of cGMP in Pharmaceutical Manufacturing
The significance of current good manufacturing practices in pharmaceutical manufacturing is paramount. Adherence to these regulations ensures that products are consistently manufactured and monitored to meet rigorous performance standards, which is crucial for protecting patient safety. A transformative case study involving AVS Life Sciences illustrates this point: the company successfully assisted a leading biotechnology firm in upgrading their manufacturing space from a Biosafety Level 1 GMP facility to a Level 2 GMP facility, completing the project on schedule and within budget. This upgrade not only guaranteed adherence to regulatory standards but also improved the quality assurance processes within the organization.
Non-compliance can result in the distribution of contaminated or ineffective medications, posing serious risks to public health. Furthermore, compliance with current good manufacturing practices enhances public confidence in pharmaceutical products, assuring consumers that the medications they obtain are both safe and effective. Firms that emphasize good manufacturing practices, such as the one backed by AVS Life Sciences, not only reduce the chances of regulatory fines and product withdrawals but also safeguard their reputation, ultimately resulting in greater market success. For instance, a landmark study revealed that implementing advanced analytical tools reduced adverse event reporting times by 86%, demonstrating the direct benefits of strong regulatory measures. Additionally, organizations that clearly invest in good manufacturing practices establish stronger connections with patients and healthcare providers, promoting brand loyalty and improving their market position.
During the project, important lessons were learned regarding the barcode scanner issue, where some cameras were installed upside down, leading to overlooked anomalies in test results. This experience prompted the QC laboratory team and Quality team to evaluate their business processes, identifying gaps that allowed for unreliable test results. As the worldwide pharmaceutical industry is expected to hit $1.5 trillion by 2028, the significance of current good manufacturing practices in guaranteeing standards and safety cannot be exaggerated. Compliance with regulations outlined in 21 CFR Part 50/56/312 and 21 CFR Part 11 is critical for navigating the regulatory landscape, and the consequences of non-compliance can include product recalls and significant financial damage.
Outline Regulatory Oversight and Compliance Mechanisms for cGMP
Regulatory supervision for current good manufacturing practices is predominantly conducted by the FDA, which enforces compliance through a meticulous series of inspections and audits of production facilities. These inspections evaluate adherence to current good manufacturing practices, focusing on production processes, quality control systems, and documentation practices. Companies are required to maintain comprehensive records of their manufacturing processes, which are rigorously scrutinized during these inspections. Non-compliance can result in severe consequences, including warning letters, fines, and potential suspension of manufacturing operations.
For instance, the FDA has documented deficiencies in over 5,000 Form 483s, highlighting prevalent issues such as failure to adhere to written instructions and inadequacies in examining deviations. Additionally, the FDA provides guidance documents to assist companies in understanding and implementing current good manufacturing practices effectively, ensuring they navigate the complexities of regulatory obligations.
Recent statistics reveal that from 2019 to 2023, the FDA's issuance of warning letters has surged significantly, reflecting increased scrutiny on manufacturing practices. This trend underscores the necessity for drug companies to adopt proactive compliance strategies to avert financial losses and maintain operational integrity.
AVS Life Sciences offers comprehensive GXP regulatory services, concentrating on critical areas such as GMP audits for APIs, drug products, and testing facilities. Their expertise in quality management and regulatory compliance guarantees that drug companies can successfully meet the stringent requirements established by regulatory authorities.
Discuss Consequences of Non-Compliance with cGMP
Non-compliance with current good manufacturing practices presents serious and complex challenges for pharmaceutical firms. Regulatory actions can manifest as:
- Warning letters
- Substantial fines
- Mandatory recalls of defective products
In extreme cases, individuals within the organization may face criminal charges, highlighting the gravity of these violations. The reputational damage associated with regulatory breaches is profound, often resulting in a significant erosion of consumer confidence and market share. Companies subjected to FDA sanctions, for instance, frequently experience declines in stock prices and investor confidence, which can further worsen their financial situation.
The economic repercussions are considerable; addressing violations of current good manufacturing practices can lead to increased operational costs, including necessary facility upgrades and comprehensive employee training. Ultimately, the financial and operational consequences of non-compliance threaten a company's long-term viability in the competitive pharmaceutical landscape, making adherence to current good manufacturing practices not just a regulatory obligation but a crucial business strategy.
Conclusion
Current good manufacturing practices (cGMP) are essential for ensuring the safety, quality, and efficacy of pharmaceutical products. Enforced by the FDA, these regulations establish the standard for manufacturing processes and controls, highlighting the necessity for continuous improvement and the adoption of the latest technologies. The significance of cGMP transcends mere compliance; it is a pivotal element of operational excellence and the trust vested in the pharmaceutical industry.
Key insights throughout the article reveal that strict adherence to cGMP not only safeguards patient safety but also bolsters operational efficiency and brand reputation. Case studies exemplify the tangible benefits of compliance, including:
- Enhanced quality assurance processes
- Decreased adverse event reporting times
Furthermore, the ongoing scrutiny from regulatory bodies underscores the imperative for companies to implement proactive compliance strategies, ensuring they meet stringent standards and evade severe penalties linked to non-compliance.
As the pharmaceutical landscape evolves, the importance of current good manufacturing practices cannot be overstated. Organizations must recognize that investing in cGMP compliance is not just a regulatory obligation but a strategic necessity that cultivates public confidence and drives market success. By prioritizing these practices, companies can protect public health, improve product quality, and ultimately excel in a competitive environment.
Frequently Asked Questions
What are Current Good Manufacturing Practices (cGMP)?
Current Good Manufacturing Practices (cGMP) are essential regulations established by the Food and Drug Administration (FDA) to ensure the quality, safety, and efficacy of pharmaceutical products. They set minimum standards for manufacturing processes, facilities, and controls involved in drug production.
Why is the term 'current' important in cGMP?
The term 'current' emphasizes the necessity of utilizing up-to-date technologies and methodologies to maintain compliance with manufacturing practices.
What critical areas do cGMP regulations cover?
cGMP regulations encompass critical areas such as personnel qualifications, sanitation protocols, equipment maintenance, and stringent quality control measures.
What is the significance of cGMP in the pharmaceutical industry?
cGMP is vital for preventing contamination and upholding product integrity in the pharmaceutical industry, where the stakes are particularly high.
What is the projected growth of the biologics market by 2025?
The biologics market is projected to grow at a compound annual growth rate of 15% by 2025, highlighting the increasing complexity and necessity for compliance with cGMP.
How does the FDA ensure compliance with cGMP?
The FDA demonstrates its commitment to enforcing cGMP regulations through continuous updates and revisions to guidelines, ensuring manufacturers are equipped to handle evolving industry challenges.
What are the benefits of implementing cGMP?
Successful implementation of cGMP enhances product standards and leads to significant improvements in efficiency and compliance outcomes in pharmaceutical production.
What challenges do companies face in applying cGMP uniformly across the industry?
While larger companies have made advancements in statistical applications under cGMP, there remains a critical need for uniform application across the industry.
How does the evolving medicinal landscape affect cGMP?
The advent of novel treatments, such as monoclonal antibodies, presents unique challenges that necessitate a robust quality management system, underscoring the importance of cGMP.
Why are GMP regulations important beyond compliance?
GMP regulations are vital for ensuring that medical products are manufactured to the highest standards, safeguarding public health and maintaining trust in the industry.
What does AVS Life Sciences exemplify in relation to cGMP?
AVS Life Sciences exemplifies the effectiveness of adhering to cGMP practices, showcasing a commitment to excellence and an impressive 80% repeat business rate, positioning itself as a leading provider of management and regulatory compliance solutions in the life sciences sector.