cgmp vs gmp: Key Differences and Impact on Compliance
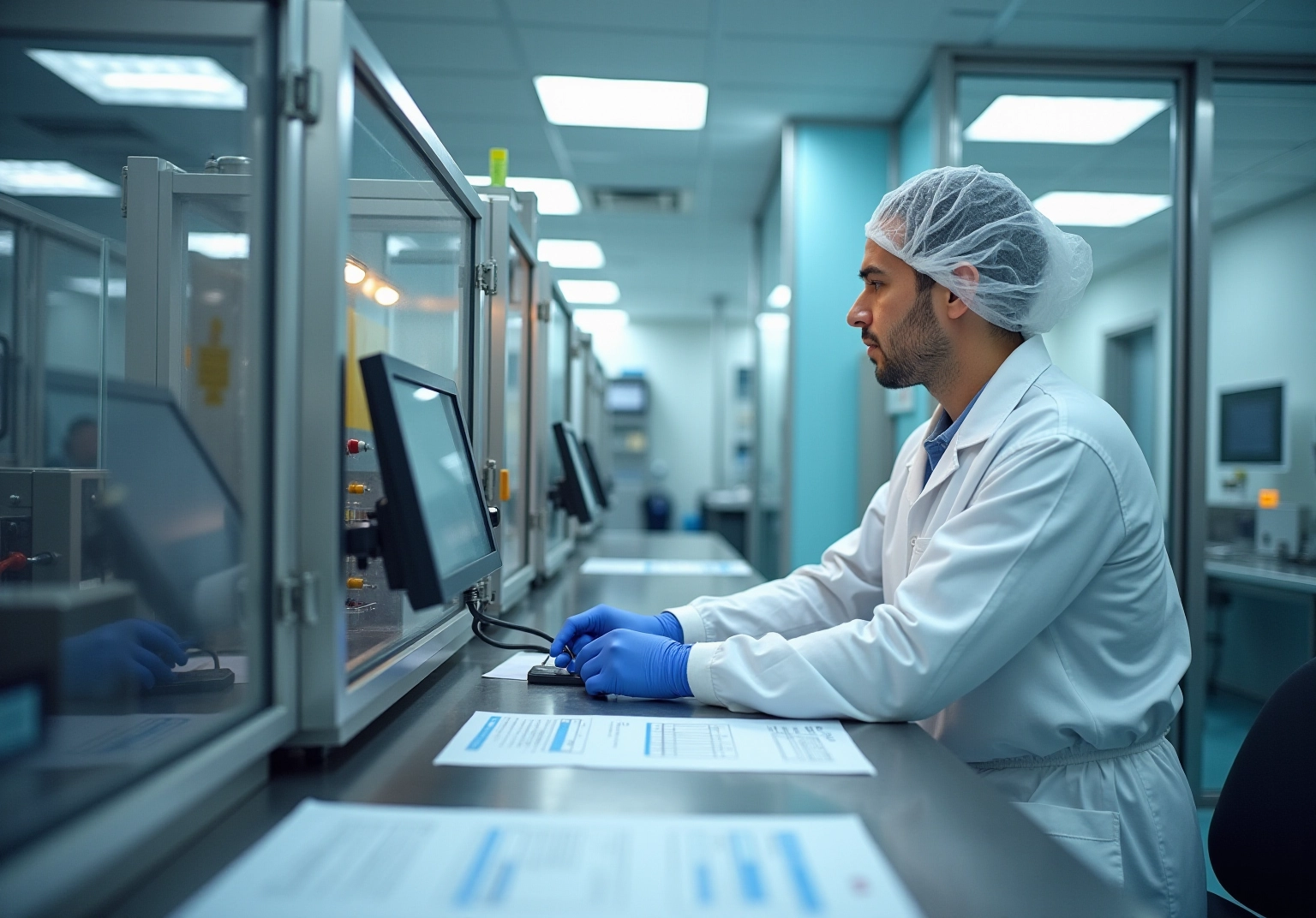
Overview
This article delineates the fundamental distinctions between Good Manufacturing Practices (GMP) and current Good Manufacturing Practices (cGMP), underscoring how cGMP integrates modern technologies and a proactive compliance approach. While GMP is frequently static, potentially resulting in inefficiencies, cGMP fosters an environment of continuous improvement and innovation. This evolution not only enhances product quality but also boosts operational efficiency within the pharmaceutical industry, positioning organizations for greater success. As the industry evolves, embracing cGMP becomes essential for maintaining compliance and achieving excellence.
Introduction
The landscape of pharmaceutical manufacturing is undergoing a significant transformation as organizations grapple with the implications of Good Manufacturing Practices (GMP) versus current Good Manufacturing Practices (cGMP). These frameworks are not merely regulatory checkboxes; they are essential to ensuring product quality and safety in an industry where the stakes are incredibly high. This article delves into the critical distinctions between GMP and cGMP, highlighting how embracing modern methodologies can enhance compliance and operational efficiency. As companies strive to align with evolving standards, they encounter both challenges and opportunities in navigating this complex regulatory terrain.
Define GMP and cGMP: Core Concepts and Terminology
Good Manufacturing Practices (GMP) and the differences highlighted in cgmp vs gmp represent the regulations and guidelines that ensure products are consistently produced and controlled in accordance with quality standards. These practices are designed to mitigate risks inherent in pharmaceutical manufacturing that cannot be eliminated solely through testing the final product.
In contrast, the principles upheld by current Good Manufacturing Practices, commonly referred to as cgmp vs gmp, emphasize the necessity for manufacturers to adopt modern technologies and systems to maintain standards. Current regulations are more flexible, reflecting the latest advancements in manufacturing processes and quality assurance, thereby ensuring that products remain safe, effective, and of high quality throughout their lifecycle.
The key distinction in cgmp vs gmp lies in the 'current' aspect of GMP, which necessitates that companies remain updated on the latest industry standards and technologies.
At AVS Life Sciences, we implement these principles through our comprehensive management and regulatory compliance solutions, ensuring that our clients not only meet but exceed GMP standards. Our expertise in life sciences consulting empowers organizations to embrace the latest technologies and practices, significantly enhancing their compliance and product quality.
Contrast GMP and cGMP: Key Differences and Enhancements
The distinction of cgmp vs gmp hinges primarily on flexibility and a commitment to modern methodologies. GMP is often perceived as a static set of guidelines, whereas current good manufacturing practices advocate for continuous improvement and the integration of innovative technologies.
For example, regulations mandate that producers establish management systems that are routinely updated to meet contemporary standards, a requirement not explicitly outlined in GMP. Furthermore, these guidelines emphasize proactive risk management and quality assurance, empowering organizations to identify and mitigate potential issues before they compromise product quality.
This shift from a reactive to a proactive approach is crucial for ensuring compliance in the ever-evolving pharmaceutical sector. Companies that have successfully transitioned from GMP to current good manufacturing practices have reported enhanced operational efficiencies and improved safety of their products, which highlights the advantages of understanding cgmp vs gmp in today’s competitive environment.
Evaluate the Impact of GMP vs cGMP on Pharmaceutical Operations
The comparison of cGMP vs GMP profoundly influences pharmaceutical operations. Companies adhering to GMP often encounter challenges stemming from outdated practices that fail to align with modern technologies, which can result in inefficiencies and an increased risk of non-compliance. In contrast, organizations that implement cGMP vs GMP are strategically positioned to leverage contemporary manufacturing technologies, thereby enhancing product standards and operational efficiency.
A notable example is AVS Life Sciences, which recently assisted a leading biotechnology company in upgrading its manufacturing space from a Biosafety Level 1 GMP facility to a Level 2 GMP facility. This transformation not only ensured compliance with current standards but also strengthened assurance procedures.
During this upgrade, challenges such as the misalignment of barcode scanner cameras were identified, initially causing anomalies in test results. This oversight underscored the critical need for thorough testing and robust monitoring systems.
When comparing cGMP vs GMP, it is evident that cGMP-compliant companies frequently utilize automated systems for monitoring and documentation, minimizing human error and ensuring consistent standards. Furthermore, adherence to good manufacturing practices often leads to fewer regulatory inspections and a diminished likelihood of receiving citations, as these firms are perceived as proactive in their assurance efforts.
The successful upgrade by AVS Life Sciences exemplifies how embracing cGMP vs GMP can drive operational excellence and foster the development of innovative therapies that enhance patient outcomes. The significant lessons learned from this project have inspired the QC laboratory group and Assurance team to evaluate their business processes, ensuring continuous improvement in standards.
Assess Benefits and Challenges of GMP and cGMP Implementation
Implementing Good Manufacturing Practices (GMP) lays a robust foundation for ensuring item standards and safety, yet it presents challenges, particularly in adapting to new technologies. Conversely, current Good Manufacturing Practices (cGMP) offer a more dynamic framework that fosters innovation and continuous improvement, ultimately enhancing quality and operational efficiency.
However, the transition to cGMP can be resource-intensive, requiring significant investments in training, technology, and process redesign. Organizations must also navigate the complexities of adhering to evolving regulations, which can be particularly daunting. For instance, companies that fail to comply with cGMP standards risk substantial financial repercussions, including regulatory penalties and product recalls.
Moreover, maintaining comprehensive documentation of all activities, processes, and tests conducted during production is crucial for compliance with cGMP. The decision regarding cGMP vs GMP depends on an organization's specific needs, available resources, and unwavering commitment to excellence.
As demonstrated by the 80% repeat business rate of AVS Life Sciences, organizations that adeptly navigate these challenges can cultivate a trustworthy reputation and achieve long-term success in the competitive pharmaceutical landscape. AVS Life Sciences provides comprehensive quality management and regulatory compliance solutions that assist organizations in effectively implementing cGMP standards, ensuring compliance while enhancing operational efficiency.
Conclusion
The exploration of cGMP versus GMP reveals a critical evolution in manufacturing practices within the pharmaceutical industry. Good Manufacturing Practices lay the groundwork for quality assurance, while current Good Manufacturing Practices emphasize the necessity for ongoing adaptation and integration of modern technologies. This shift not only enhances compliance but also drives operational excellence, ensuring that products are consistently safe and effective.
Key insights from the comparison highlight that cGMP fosters a proactive approach to risk management and quality assurance, allowing organizations to stay ahead of potential issues. The transition to cGMP, although resource-intensive, ultimately leads to improved efficiencies, fewer regulatory challenges, and a stronger reputation in the competitive landscape. Companies that embrace these advanced practices are better positioned to meet contemporary standards and innovate within their operations.
In a rapidly evolving industry, the significance of understanding the differences between GMP and cGMP cannot be overstated. Organizations are encouraged to assess their current practices and consider the benefits of transitioning to cGMP. By doing so, they not only enhance their compliance and operational capabilities but also contribute to the overall advancement of pharmaceutical manufacturing, ultimately benefiting patient outcomes and public health.
Frequently Asked Questions
What do GMP and cGMP stand for?
GMP stands for Good Manufacturing Practices, while cGMP refers to current Good Manufacturing Practices.
What is the purpose of GMP and cGMP?
GMP and cGMP are regulations and guidelines designed to ensure that products are consistently produced and controlled according to quality standards, mitigating risks in pharmaceutical manufacturing.
How do GMP and cGMP differ?
The key distinction is that cGMP emphasizes the necessity for manufacturers to adopt modern technologies and systems to maintain standards, whereas GMP may not reflect the latest advancements.
Why is the 'current' aspect important in cGMP?
The 'current' aspect requires companies to stay updated on the latest industry standards and technologies to ensure products remain safe, effective, and of high quality throughout their lifecycle.
How does AVS Life Sciences implement GMP and cGMP principles?
AVS Life Sciences implements these principles through comprehensive management and regulatory compliance solutions, helping clients meet and exceed GMP standards.
What benefits does AVS Life Sciences offer in terms of compliance?
AVS Life Sciences provides expertise in life sciences consulting, enabling organizations to embrace the latest technologies and practices, which enhances their compliance and product quality significantly.